Basement renovation has become increasingly popular among Canadian homeowners in recent years. Many houses across the country, from the coastal regions of British Columbia...
Top 7 Common Mistakes When Installing Attic Insulation

Did you know that up to 40% of a home’s heating and cooling energy can be lost through a poorly insulated attic? This surprising statistic underscores the critical role that proper attic insulation plays in maintaining a comfortable and energy-efficient home.
While many homeowners recognize the importance of insulating their attics, the quality of installation can make or break its effectiveness. Proper installation ensures that insulation performs at its peak, creating a consistent thermal barrier that keeps warm air in during winter and out during summer. This not only enhances comfort but also leads to significant energy savings over time.
In this post, we’ll explore common mistakes that occur during attic insulation installation and provide practical tips on how to avoid them. By understanding these pitfalls, you can ensure your attic insulation project delivers maximum benefit for your home’s energy efficiency and your family’s comfort.
Choosing the Wrong Type of Insulation

Mistake Description: One of the most common mistakes in attic insulation is selecting an inappropriate type of insulation for the specific needs of the home. This often occurs due to a lack of understanding about the different insulation materials available and their unique properties. Homeowners may choose based solely on cost or familiarity, without considering factors such as climate, attic structure, or local building codes.
Consequences: Selecting the wrong insulation can lead to several issues:
- Reduced energy efficiency, resulting in higher heating and cooling costs
- Moisture problems, potentially leading to mold growth or structural damage
- Poor sound insulation, especially in urban areas
- Decreased home comfort due to inconsistent temperatures
- Potential code violations, which could cause problems during home inspections or sales
Solution: To choose the right type of insulation:
- Assess your climate: Different insulation types perform better in certain climates. For example, closed-cell spray foam is excellent for humid areas, while fiberglass batts might be suitable for drier regions.
- Consider R-value requirements: Check local building codes for minimum R-value requirements in your area. Choose an insulation type that can achieve this value within your attic’s space constraints.
- Evaluate installation method: Some insulations, like blown-in cellulose, are easier to install in hard-to-reach areas, while others, like rigid foam boards, might be better for attics with limited space.
- Account for moisture concerns: If your attic is prone to moisture, consider insulation with moisture-resistant properties or pair your insulation choice with proper ventilation solutions.
- Factor in long-term costs: While some insulation types may be more expensive upfront, they could offer better long-term energy savings and durability.
- Consult professionals: When in doubt, consult with a certified insulation contractor or energy auditor. They can assess your specific needs and recommend the most suitable insulation type for your attic.
By carefully considering these factors, you can avoid the pitfall of choosing the wrong insulation and ensure your attic is properly protected for maximum efficiency and comfort.
Ignoring the R-Value
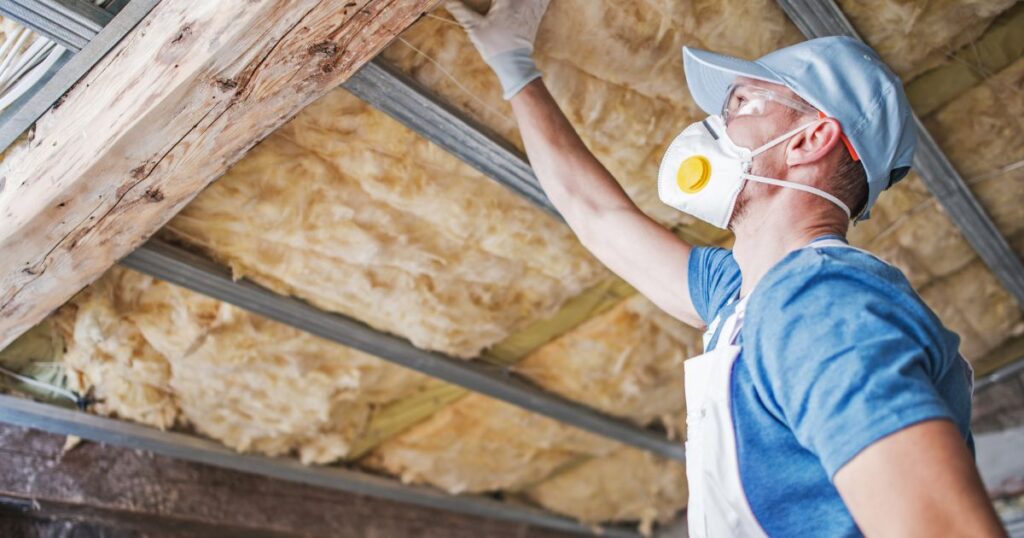
Mistake Description: A critical error in attic insulation is overlooking or misunderstanding the R-value. The R-value measures insulation’s ability to resist heat flow – the higher the R-value, the greater the insulating effectiveness. Many homeowners fail to consider this crucial factor, instead focusing solely on the thickness of the insulation or its cost.
Consequences: Disregarding the R-value can lead to:
- Inadequate insulation performance, resulting in higher energy bills
- Discomfort due to inconsistent indoor temperatures
- Potential building code violations, as many areas specify minimum R-value requirements
- Increased strain on HVAC systems, potentially shortening their lifespan
- Reduced energy efficiency of the entire home
Solution: To ensure you’re using the appropriate R-value:
- Understand your climate zone: R-value requirements vary based on geographic location. The U.S. Department of Energy provides recommendations for different climate zones.
- Check local building codes: These often specify minimum R-values for attic insulation. Ensure your insulation meets or exceeds these standards.
- Consider additive R-values: If you’re adding insulation to existing material, remember that R-values are additive. Calculate the total R-value of all layers combined.
- Don’t over-compress insulation: Compressing insulation reduces its R-value. Ensure you have enough space to install the full recommended thickness.
- Account for diminishing returns: While higher R-values generally mean better insulation, there’s a point of diminishing returns. Consult with a professional to find the optimal R-value for your situation.
- Factor in other home characteristics: The ideal R-value can also depend on factors like your home’s air sealing, HVAC efficiency, and overall construction.
- Use the Department of Energy’s Zip Code Insulation Calculator: This tool can help you determine the most cost-effective R-value for your specific location and home type.
By paying close attention to R-value, you can ensure your attic insulation performs effectively, keeping your home comfortable and energy-efficient year-round.
Inadequate Air Sealing
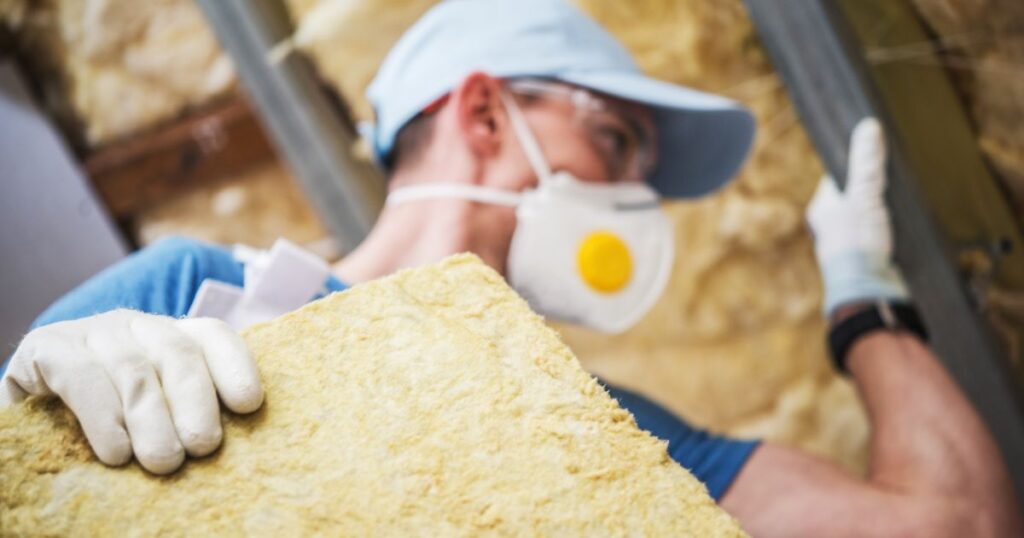
Mistake Description: A critical error often overlooked in attic insulation projects is failing to properly air seal before installing insulation. Air sealing involves closing off any gaps, cracks, or openings that allow air to move between the living space and the attic. Many homeowners and even some contractors skip this crucial step, focusing solely on laying down insulation.
Consequences: Neglecting air sealing can result in:
- Reduced insulation effectiveness, as air movement can bypass even the best insulation
- Increased energy costs due to conditioned air escaping into the attic
- Moisture problems, as warm air can carry humidity into the attic, potentially leading to mold or rot
- Ice dams in cold climates, caused by warm air melting snow on the roof
- Decreased indoor comfort due to drafts and inconsistent temperatures
- Potential for pollutants and allergens to enter living spaces from the attic
Solution: To ensure proper air sealing:
- Conduct a thorough inspection: Before insulating, carefully examine the attic for any gaps or openings. Pay special attention to areas around chimneys, vents, electrical wires, and where walls meet the attic floor.
- Use appropriate materials: Apply caulk for small gaps (less than 1/4 inch) and spray foam for larger openings. Use fire-rated materials around heat sources like chimneys and recessed lights.
- Address common trouble spots:
- Seal around attic hatches or doors
- Install foam gaskets behind outlet covers on exterior walls
- Caulk around windows and doors
- Seal any gaps around plumbing or electrical penetrations
- Consider professional testing: A blower door test can help identify less obvious air leaks and verify the effectiveness of your sealing efforts.
- Don’t forget about proper ventilation: While sealing air leaks, ensure you maintain proper attic ventilation to prevent moisture buildup.
- Use visual aids: Smoke pencils or infrared cameras can help detect air leaks that might not be visible to the naked eye.
- Tackle the attic floor: Pay special attention to sealing the attic floor, as this is where most air leakage occurs between living spaces and the attic.
By thoroughly air sealing before installing insulation, you’ll significantly enhance the performance of your attic insulation, leading to improved energy efficiency, comfort, and long-term protection of your home’s structure.
Blocking Ventilation

Mistake Description: A common yet serious mistake in attic insulation is inadvertently blocking ventilation. This often occurs when insulation is installed without regard for existing vents, soffit areas, or other ventilation systems. Homeowners or inexperienced installers may believe that sealing off these areas will improve insulation performance, but this approach is misguided and potentially harmful.
Consequences: Obstructing attic ventilation can lead to several problems:
- Moisture accumulation, which can lead to mold growth and wood rot
- Reduced lifespan of roofing materials due to excess heat and moisture
- Ice dam formation in cold climates
- Increased energy costs from heat buildup in summer months
- Potential voiding of roof warranties
- Poor indoor air quality if mold develops
- Structural damage to the roof deck over time
Solution: To maintain proper ventilation while insulating:
- Understand your attic’s ventilation system: Familiarize yourself with the locations of soffit vents, ridge vents, gable vents, and any other ventilation components in your attic.
- Use attic baffles: Install baffles (also known as ventilation chutes) before adding insulation. These create a clear channel for air to flow from the soffit vents up to the ridge vent.
- Keep soffit vents clear: Ensure that insulation doesn’t cover or block soffit vents. Maintain a gap of at least 1-2 inches between the insulation and the roof deck.
- Balance intake and exhaust: Aim for a balanced system with equal amounts of low (intake) and high (exhaust) ventilation.
- Consider a professional assessment: If you’re unsure about your attic’s ventilation needs, consult with a roofing or insulation professional.
- Use the right insulation technique: For example, when using blown-in insulation, be careful not to overfill areas near vents.
- Regularly inspect ventilation pathways: After insulation is installed, periodically check to ensure vents remain unobstructed.
- Don’t forget about recessed lights: Use insulation covers for recessed lights to maintain proper clearance and ventilation.
By maintaining proper attic ventilation while insulating, you’ll create a balanced system that effectively manages temperature and moisture, prolonging the life of your roof and ensuring the efficiency of your insulation.
Compressing the Insulation
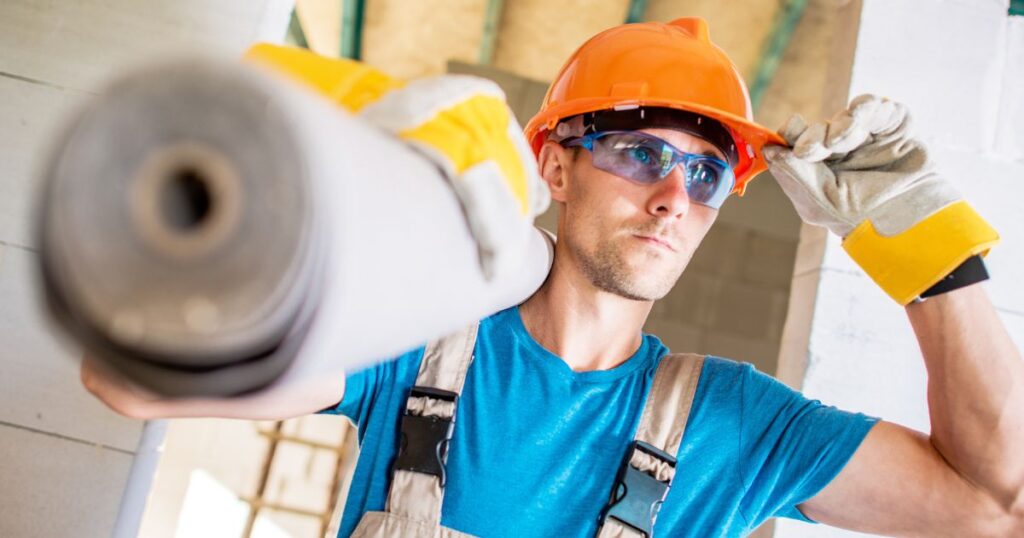
Mistake Description: A frequent error in attic insulation installation is compressing the insulation material. This often occurs when trying to fit thick insulation into a space that’s too small, or when storing items on top of the insulation. Many people mistakenly believe that compressing insulation will increase its effectiveness, but the opposite is true.
Consequences: Compressing insulation leads to several issues:
- Reduced R-value: Compression significantly decreases the insulation’s R-value, reducing its effectiveness
- Decreased energy efficiency: As insulation performance drops, more heat transfers through the material, increasing energy costs
- Uneven insulation: Compressed areas create cold spots, leading to inconsistent temperatures throughout the home
- Potential moisture problems: Compressed areas may allow for increased condensation, potentially leading to mold or mildew
- Wasted money: You pay for the full R-value of the insulation, but don’t get the full benefit when it’s compressed
Solution: To avoid compressing insulation:
- Choose the right thickness: Select insulation with a thickness appropriate for the space available. Don’t try to squeeze in a thicker product thinking it will perform better.
- Use multiple layers: If you need a higher R-value, consider using multiple layers of thinner insulation rather than compressing a thicker layer.
- Install correctly: Follow manufacturer guidelines for installation. For batts, fit them snugly between joists without forcing or compressing.
- Avoid walking on insulation: When working in the attic, use walking boards to distribute your weight and prevent compression.
- Don’t store items on insulation: Create a separate storage area with a raised floor if you need to use your attic for storage.
- Use blow-in insulation for irregular spaces: In areas with obstructions or irregular shapes, consider blow-in insulation which can fill spaces without compression.
- Install insulation baffles: These maintain space between the insulation and the roof deck, preventing compression and ensuring proper ventilation.
- Consider raised heel trusses: If building or extensively renovating, raised heel trusses allow for full-thickness insulation even at the eaves.
By avoiding compression, you ensure that your insulation performs at its rated R-value, maximizing energy efficiency and comfort in your home. Remember, when it comes to insulation, fluffier is better – don’t be tempted to pack it down!
Failing to Use a Vapor Barrier

Mistake Description: A critical oversight in attic insulation is neglecting to install a vapor barrier when needed. Vapor barriers are materials that inhibit the movement of moisture through walls, ceilings, and floors. Many homeowners and some contractors overlook this crucial component, especially in climates where moisture control is essential. The necessity and placement of vapor barriers can vary depending on your local climate and building practices.
Consequences: Omitting a necessary vapor barrier can lead to several problems:
- Moisture accumulation in insulation, reducing its effectiveness
- Potential for mold and mildew growth in the attic and wall cavities
- Wood rot and structural damage over time
- Decreased indoor air quality due to mold spores
- Increased energy costs as damp insulation loses its insulating properties
- Ice dam formation in cold climates
- Peeling paint or wallpaper in living spaces
Solution: To effectively use vapor barriers:
- Understand your climate: Vapor barriers are typically more crucial in cold climates where indoor humidity can migrate into colder attic spaces. In hot, humid climates, vapor barriers may be installed differently or even omitted.
- Know where to install: In cold climates, vapor barriers typically go on the warm side of the insulation (facing the living space). In hot, humid climates, they may be omitted or placed on the exterior side.
- Choose the right material: Common vapor barriers include polyethylene sheets, kraft paper-faced fiberglass batts, or special vapor barrier paints.
- Ensure proper installation: The vapor barrier should be continuous and free of holes or gaps. Seal all seams and penetrations carefully.
- Consider smart vapor retarders: These materials change their permeability based on seasonal humidity levels, offering flexibility in varying climates.
- Don’t double up: Avoid installing vapor barriers on both sides of a wall or ceiling, as this can trap moisture between layers.
- Consult local building codes: These often specify if and how vapor barriers should be used in your area.
- Address existing moisture issues: Before installing a vapor barrier, ensure any existing moisture problems in the attic are resolved.
- Pair with proper ventilation: Vapor barriers work best when combined with adequate attic ventilation to manage any moisture that does enter the space.
- Seek professional advice: If you’re unsure about vapor barrier requirements in your area, consult with a local insulation professional or building scientist.
By correctly incorporating vapor barriers into your attic insulation system when necessary, you’ll better protect your home from moisture-related issues, ensuring the longevity of your structure and the effectiveness of your insulation.
Not Accounting for Electrical and Plumbing

Mistake Description: A common oversight in attic insulation projects is failing to properly plan for and work around electrical wiring and plumbing fixtures. Many homeowners and inexperienced installers may simply lay insulation over these elements without considering the implications. This approach can lead to both safety hazards and reduced insulation effectiveness.
Consequences: Ignoring electrical and plumbing components when insulating can result in:
- Fire hazards due to overheating electrical wires
- Reduced access for future repairs or inspections
- Freezing pipes in cold climates
- Decreased overall insulation effectiveness due to gaps and voids
- Potential code violations
- Moisture problems from improperly insulated pipes
- Difficulty in detecting leaks or electrical issues
Solution: To properly insulate around electrical and plumbing components:
- Create a map: Before insulating, document the location of all wiring and plumbing in your attic. This will help you plan your insulation strategy.
- Maintain clearance around electrical fixtures: Keep insulation at least 3 inches away from recessed lighting fixtures unless they are IC-rated (Insulation Contact).
- Use wire guards: Install plastic wire guards around electrical junction boxes to prevent contact with insulation while maintaining access.
- Insulate pipes properly: Use foam pipe insulation on water pipes before adding attic insulation. This helps prevent freezing in cold climates and condensation in warm climates.
- Avoid covering knob-and-tube wiring: If your home has this older type of wiring, consult an electrician before insulating. It may need to be replaced.
- Use appropriate materials: Around chimneys and flues, use non-flammable insulation materials and maintain required clearances.
- Create pathways: If using blown-in insulation, create pathways or channels to maintain access to key electrical and plumbing components.
- Consider raised platforms: For frequently accessed areas, build raised platforms above the insulation level to maintain easy access to utilities.
- Use insulation baffles: These can help direct insulation around obstacles while maintaining proper ventilation.
- Seek professional help: If you’re unsure about working around electrical or plumbing components, consult with or hire a professional insulation contractor.
By carefully planning and executing your insulation strategy around electrical and plumbing elements, you’ll ensure a safer, more effective insulation job that complies with building codes and maintains accessibility for future maintenance.
FAQs on Mistakes When Installing Attic Insulation

Q: What is the most common mistake homeowners make when installing attic insulation?
Ans: One of the most common mistakes is choosing the wrong type of insulation. Each type of insulation has different properties, and selecting the incorrect one for your climate or specific needs can lead to inefficiency and higher energy costs.
Q: Why is the R-value important in attic insulation?
Ans: The R-value measures the insulation’s ability to resist heat flow. Higher R-values indicate better insulating properties. Using insulation with an inappropriate R-value can result in inadequate thermal performance and increased energy bills.
Q: How can I find and seal air leaks in my attic before insulating?
Ans: You can detect air leaks by checking common trouble spots like gaps around chimneys, vents, and pipes. Use caulk or spray foam to seal smaller gaps, and weatherstripping for larger areas. Performing a blower door test can also help identify leaks.
Q: What should I do to maintain proper ventilation in my attic during insulation installation?
Ans: Ensure that attic vents are not blocked by insulation. Use baffles (vent chutes) to keep insulation away from soffit vents and maintain airflow. Proper ventilation prevents moisture buildup and extends the life of your roof.
Q: What happens if insulation is compressed during installation?
Ans: Compressing insulation reduces its thickness and effectiveness. This can lead to decreased thermal performance and higher energy costs. Always install insulation loosely and avoid stepping on or packing it tightly.
Q: When is it necessary to use a vapor barrier in attic insulation?
Ans: Vapor barriers are necessary in climates with significant moisture differences between indoors and outdoors, such as in very cold or humid regions. They prevent moisture from entering the insulation, which can cause mold and reduce insulation effectiveness.
Q: How can I safely insulate around electrical wires and plumbing in my attic?
Ans: Turn off power before working near electrical wiring. Use non-combustible materials and avoid covering recessed lighting fixtures unless they are rated for insulation contact (IC-rated). Cut insulation to fit snugly around pipes without compressing it.
Q: What is the recommended thickness for attic insulation?
Ans: The recommended thickness depends on your climate zone. Generally, the U.S. Department of Energy suggests an R-value of R-38 to R-60 for attics in most parts of the country, which translates to about 10-14 inches of fiberglass or cellulose insulation.
Q: How do I insulate my attic hatch?
Ans: Use rigid foam board cut to fit the hatch and secure it with adhesive or screws. Attach weatherstripping around the edge to create an airtight seal. Consider adding a layer of batt insulation on top of the foam board for additional thermal resistance.
Q: Is it worth doing attic insulation myself, or should I hire a professional?
Ans: While DIY attic insulation can save money, it requires knowledge and precision to avoid common mistakes. If you’re unsure about any part of the process, it’s best to hire a professional to ensure proper installation and maximize energy efficiency.
Final Thoughts on Mistakes When Installing Attic Insulation
By steering clear of these common pitfalls, you can ensure that your attic insulation performs at its best, leading to significant energy savings and improved home comfort. Remember, effective insulation is not just about the material itself, but also about proper installation and attention to detail.
We encourage you to approach your attic insulation project with these insights in mind. Whether you’re planning a DIY project or hiring professionals, being aware of these potential issues will help you achieve better results.
Have you encountered any of these problems in your own home? Or perhaps you have additional tips to share? We’d love to hear about your experiences and questions in the comments below. Your insights could help fellow homeowners tackle their insulation projects more effectively.
Hey people!!!!!
Good mood and good luck to everyone!!!!!